Not all heroes wear masks – some design them
Research impact and institutes 2nd July 2020
Masks are something of a wardrobe staple right now – although few fashion houses would have predicted this six months ago. The government has advised that masks should be worn when visiting enclosed public spaces, while face coverings are now a legal requirement on public transport.
While masks have been shown to help slow the spread of coronavirus should the wearer have symptoms or be an asympthematic carrier, in hospitals they take on a whole new meaning. Not only are there the medical masks and visors that help protect those delivering care to patients on the frontline, but there are also the masks worn by patients on ventilators or receiving oxygen.
But when the masks worn by patients on oxygen come with a controlled leak that potentially fills the air with the virus, that’s quite a big problem. And that’s also where one of our engineers was able to come to the rescue.
Behind the mask
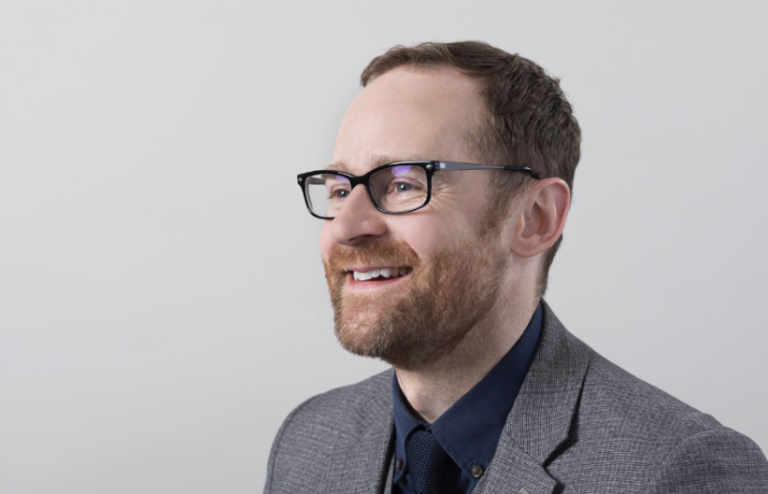
Dr Andrew Weightman is a Reader on Medical Mechatronics at the Department of Mechanical, Aerospace and Civil Engineering (MACE). During the height of the COVID-19 crisis in the UK, he was contacted by members of the intensive care unit at Wythenshawe Hospital – part of the Manchester University NHS Foundation Trust – about the issue.
The non-Invasive ventilation (NIV) machines used at the hospital are designed to deliver pressurised oxygen at high flows via a face mask as an alternative to being placed on a life support machine. The machines consume a large amount of oxygen – between 60 and 80 litres per minute. The masks have a built-in vent that allows for a leak – however, at a time when oxygen is so valuable, this is not ideal.
And then there’s the problem of the leaked air potentially carrying the airborne virus. Preventing this would mean sealing patients off in individual rooms – not practical in a busy hospital and when patients are critically ill.
The answer to the problem was to transform the vented mask into a sealed one. Dr Weightman, in partnership with Dr Brendan McGrath and Dr Peter Alexander at Wythenshawe Hospital, worked out that this small modification would mean the masks could operate at a lower oxygen flow, while the risk of the virus being released into the air was close-to eradicated.
Dr Weightman assembled a team at The University of Manchester, who used 3D printing to create an adapter that fits to the bottom of the mask in order to convert it.
“Expertise and experience”
“We have an excellent technical services team at the University and if it wasn’t for their expertise and experience we wouldn’t have been able to develop a solution so quickly,” Dr Weightman explains. “The strong links we have with Manchester University NHS Foundation Trust enabled us to assess the solution from an infection control perspective and gain rapid approval. As a team we all wanted to do something to support the people working in the NHS and the patients they are treating.”
Colleagues across the Faculty have been at the heart of the COVID-19 fight and recovery effort since lockdown was first declared in the UK. From the mathematicians modelling the potential direction of the virus to the project manager who coordinated the testing of thousands of pieces of PPE across Manchester, our University is helping to make a positive difference.
You can hear more about the efforts of our colleagues in our special COVID-19 report on The Buzz podcast.
Words – Hayley Cox
Images – Manchester University NHS, The University of Manchester
3D printingAerospace and Civil EngineeringcoronavirusCOVID-19Mechanical